There is something inherently “unsustainable” about a commercial fit-out.
After all, they are bespoke – unique to each client and space. They are materials-intensive. And they are inherently wasteful: to go in with the new, you must first rip out the old. Because fit-outs are, by definition, transitory. It is estimated that each office building will host, over its lifetime, 30 to 40 fit-outs.
So can they be “sustainable”? Or are “less unsustainable” fit-outs all we can hope for?
Of the £6bn or so spent on commercial construction each year, 11% goes on fit-outs. While most take place when an occupier takes the space, many more are done during the tenancy as well, as a retool, revamp or refresh. CBRE, for example, is currently re-fitting-out its Bond Street and City offices, following the revamp of its global head office in Los Angeles, where the focus is on passive-air, circadian lighting and germ-free surfaces.
But even the most well-intentioned, holistic, green and right-on fit-out is going to result in some unsustainable outcomes.
“The use of new materials in fit-outs will undoubtedly result in increased embodied carbon in the build,” acknowledges David Eynon, Colliers International’s senior sustainability adviser. And there will be more waste.
But Elina Grigoriou, who runs sustainable fit-out specialist Grigoriou Interiors, says that this is an obstacle, but not an insurmountable one. “We recognise that whatever activity we do, we have impacts,” she says. But, she argues, with the right approach those impacts can be minimised and the sustainability of a fit-out improved. “What we have to do is look at what the requirement is, and see how we can achieve that in a sustainable way.”
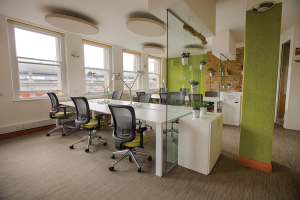
Other practitioners agree. “Although achieving carbon neutrality is challenging, there is much that can be done to move towards the goal of a sustainable fit-out,” says Mat Lown, sustainability partner at Tuffin Ferraby Taylor.
To succeed, he argues, sustainability needs to be designed-in right at the outset. Installing skylights, for example, avoids the need for artificial lighting. Using natural air circulation minimises the need for mechanical systems, which reduces energy demand. “Sustainable product lines or materials such as FSC-Certified timber should be specified if possible.”
This seems to suggest that the success of a fit-out, in terms of sustainability, actually lies in the hands of the building developer.
But what is helping occupiers and designers achieve a greater level of sustainability is a wealth of guidance that they now have at there disposal. BREEAM, which started as a way of measuring construction alone, now covers fit-out. As does LEED in the US. And then there is SKA – a fit-out-specific standard comprising more than 100 items led by RICS.
“Sustainable fit-out guides are continuing to gain traction in the marketplace,” says Nick Hillard at BNP Paribas Real Estate. “We are working with a number of high-profile clients to promote their use.”
For Hillard, the advantage of guides such as SKA is that they seek to go beyond direct effects to consider the indirect benefits of specific interventions.
“And where there are tangible cost, social and or environmental benefits,” he says, “it is inevitable that the incorporation of these guides will become mainstream considerations.”
For some, this will be an exercise in ticking boxes to get a certificate, in order to tick another box for CSR, perhaps.
Where SKA really comes into its own, Hilliard argues, is that it is concerned with not only minimising the immediate carbon impact of the fit-out, but also with generating an overall reduction in carbon emissions, water consumption and waste generation throughout the fit-out lifespan.
Grigoriou, who chairs the SKA rating technical committee, says that this aspirational element to SKA is what is really driving more and more sustainable fit-outs. “We are constantly looking for ways to not just achieve a minimum standard, but to go beyond that,” she says.
For her it is the difference between being compliant and “doing good”.
“It is one thing to install a heating system that is efficient, but to go that step further and go for one that is passive – that should be encouraged and rewarded.”
Waste is also tackled in a similar way. Since SKA was introduced, Skansen has managed to reduce the percentage of waste it sends to landfill from 32% to 5%. SKA included specific targets to reduce, for instance, the number of chairs thrown away, or how materials are reused in the scheme or recycled by someone else, instead of being binned. “We are now using SKA to encourage, for example, the retention of opening windows instead of the installation of new plant,” says Grigoriou.
Also approved of is “upcycling”, which is highly sustainable as well as achingly trendy (see ‘Everything old is new again’ below).
Interestingly, this approach means that the fit-out can be used to make the building as a whole far more sustainable than when it was built.
“Fit-outs provide an ideal opportunity to undertake sustainability and energy efficiency works,” says Eynon. “While the immediate impact will be carbon positive, the overall impact of the fit-out over its operational lifespan could be a reduction in carbon emissions that would otherwise have been generated should the fit-out not have occurred.”
Indeed, fit-outs are now increasingly being used to improve insulation levels, or install energy-efficient controls. “Implementation of these measures will ultimately drive the operational energy consumption of the space down,” Eynon points out.
Not that we should get carried away. “It is not a one-stop shop,” says Grigoriou. “You can’t use this as a way to fix every inefficient building.”
The reason for that is simple: most office blocks, or even shopping centres, are multi-tenanted. One may chose to execute its fit-out with all the environmental awareness of a Greenpeace chapter, but its co-habitants may be less enlightened and opt for acres of MDF. And even if a landlord uses green lease provisions to force their hand, unless all the fit-outs happen in harmony a truly sustainable result will be tricky to achieve.
“Tenancies have the opportunity to constantly improve and refine,” says Grigoriou. “But the passivity of the building is still down to the landlord.”
But, as Eynon says, as long as sustainability is factored in from the beginning and is the priority for everyone involved, “fit-outs can be ‘green’”.
Everything old is new again
One way of ensuring your fit-out is a sustainable as possible is to embrace cutting-edge technology. But there is another way: go retro.
At the Enterprise Centre at the gateway of the University of East Anglia in Norwich, the Adapt Low Carbon Group has stated its intent to create the greenest commercial building in Britain.
In terms of the construction, the £11.6m building is designed as a carbon sink, aiming at BREEAM Outstanding and Passivhaus certification, and using mostly recycled materials. But it is the fit-out that aims at sustainability by embracing the recent trend for upcycling.
The floors are timber, resting on a screed made from recycled glass and second-hand rubber. Even the lino is “green”, made in Scotland from a mix of linseed oil and hessian matting. And, in a flash of hipster inspiration, most of the furniture is also second-hand – or, as Adapt puts it, “pre-loved”. The chairs have been cannibalised from the UEA and reupholstered, the desks and sofas are being refurbished and reused. Even the reception desk is a hand-me-down – albeit a Norman Foster designed hand-me-down – as it originally stood in the nearby Sainsbury Centre.
Grosvenor has also recently begun using upcycled furniture in some of its recently retrofitted properties. “Fit-outs may never be totally green but there is no reason why they can’t begin that journey,” says Victoria Herring, director of refurbishment and retrofit at Grosvenor.